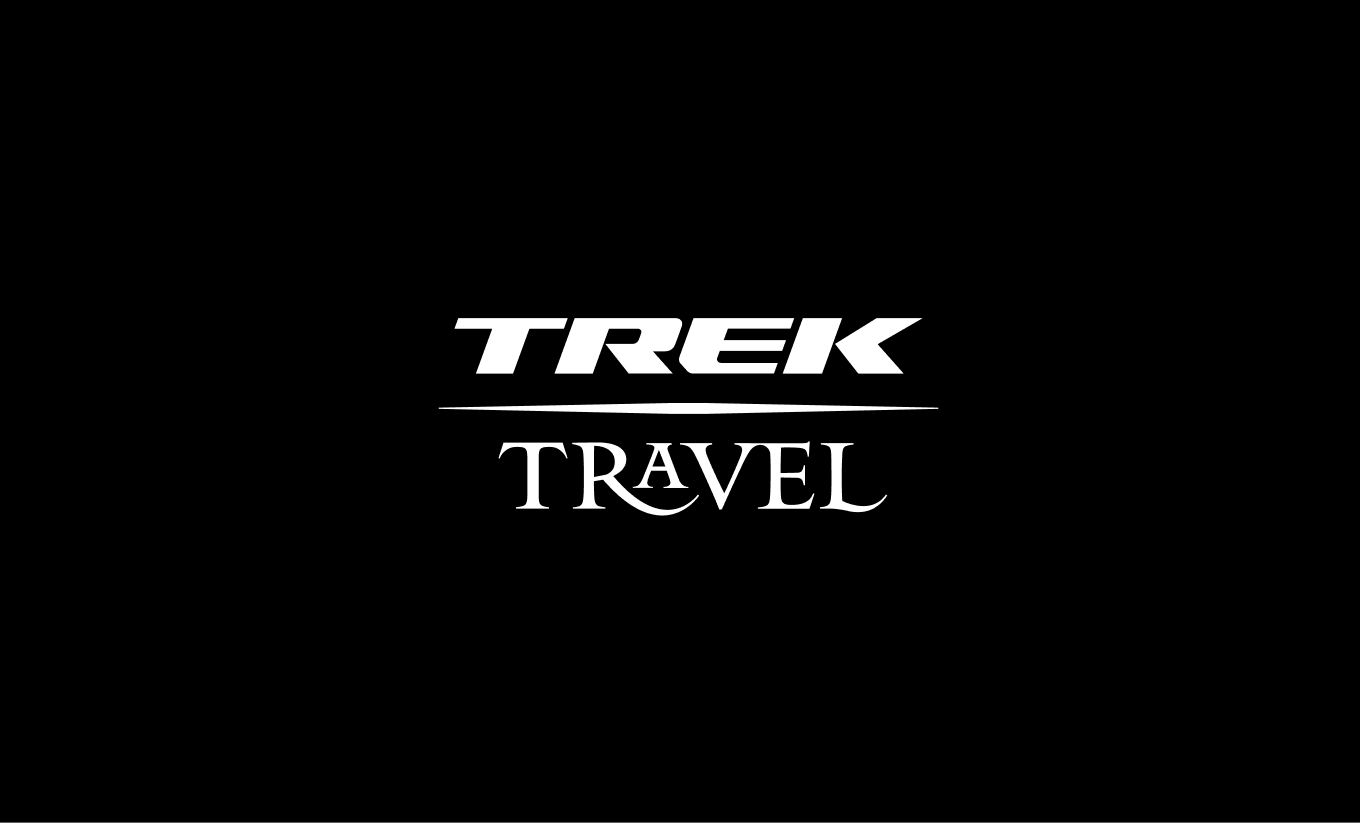
How many bikes does a person really need? The old joke makes the answer a moving target: N + 1, with N being the number of bikes already stuffed into your garage. But would that equation be different if you built one bike, from the ground up, with the exact spec, color, gearing, and fit you want, without compromise? If you got to build your one bike?
That’s the idea behind Project One: build one bike at a time, for one rider at a time. A bike unlike all others. Every wish and whim considered. trek’s custom bike program was launched to the cycling world over ten years ago. It was a daring departure for a large bike manufacturer, allowing customers to specify their individual bike’s part and color. Upsetting our busy paint and production line was risky, and creating a custom shop alongside it was definitely a bold move–one that has since gained fans across the world.
Fast forward a decade, and ever-increasing demand has warranted a new $2 million paint lineat Trek that must be seen to be believed. Paint Manufacturing Engineer Bob Seibel has been researching paint plants for several years now, including custom paint lines at similar businesses like the Harley-Davidson Motor Company in nearby Milwaukee. Bob rides a Harley, and is always happy to visit the mother ship–but this time, the objective was to solidify plans for the best painting line in the industry. One of the first requirements he identified was the need for a specific and separate location for his crew of painters.
“Before the new paint line, P1 painters never had their own space: it had always been shared with the mainline work, with custom stuff done on a second shift. Now we have a dedicated Project One paint facility; their own booths where they don’t have to close up, put away all their equipment at the end of the night only to have to take it all back out to start up the next day. Now they can just paint. They’re at home.”
But space was only the start. The real bottom line goal for the new paint booth was that we wanted to free up the artisan painters from the more technical and uncreative aspects of coatings. Changing colors, cleaning lines, painting undercoats. These things require more precision than artistry, so the new paint line is an amazing mix of technology and art, anchored by a high-tech, incredibly precise paint robot. The artists and the robot get along really well. We robotically cover the mundane tasks and keep our painters focused on the art, the beauty–the things that make Project One more than a paint job.
The frames that receive this artistry are molded from raw carbon just down the hall and up the stairs from the new paint line. There the raw carbon frames are bonded, cured, and checked for perfect alignment.
Only then can the finishing process begin. Frames are first sandblasted, then joints and bond lines are hand-sanded with care. Not a single speck of that sanding dust, Bob Seibel takes care to point out, will ever make its way into the paint booth.
Before painters enter the glass-walled booth, they don paper coveralls and pass through air showers and other contaminant removal methods to remove dust and impurities–the number one cause of paint imperfections–from all operators and frames that enter. Nothing gets in the way of a perfect finish.
“With Project One, the finishes are unbelievably meticulous. Take the U5 Vapor Coat. U5 stands for under five grams. Literally less than five grams of finished paint is applied to the frame before it’s done. A typical paint weight of a frame is easily 100 grams, if not more, because your sole focus is a smooth, flawless finish. But here we’re talking five grams or less for a paint finish, that’s astounding–it’s nothing! There is absolutely no margin for error–the coating can’t hide anything. Part of it is sandblasted, to have a matte feel and look, and the other parts are contrasted. It’s a really special look.”
Which is the whole point of Project One. We like to do special things here. Often it’s for one of the great athletes who ride Trek. Project One graphic designer Brian Lindstrom recently completed a special bike for Jens Voigt.
“Jens is very cool to work with. He had a lot of great ideas about what he wanted. We sat down in a cafe in Berlin and he started sketching ideas that he had, all the different milestones that he wanted to include on the bike that we could work on. The result was a design that reflected points in his career, so it was cool that, as fans, we can thank him for it.
I love doing athlete bikes–or it could be an entire identity for a new team, like for Trek Factory Racing: design the logo, get it all out there, color them up.”
Rarer than the athlete bikes are the fully custom civilian jobs, only endeavored when the custom queue is uncharacteristically short and the budget necessarily long. Take the skeletal bike the Project One team created for an orthopedic surgeon in New York. The doctor was a triathlete, and wanted the full custom treatment for his Speed Concept. Project One Guru (yes, that’s his title) Eric Maves recalls:
“We played off the fact that he was an orthopedic surgeon. He wanted a skeletal-type paint scheme on the bike. His main job is doing artificial joints, so he somehow wanted to integrate those into the skeletal system. I had this idea: what if we made it like an X-ray? We used the X-rays of the son of one of our painters as our benchmark. Artificial joints show up on an X-ray completely different from bone, so we went for that effect on the piece. It was intense, like 40 hours of paint labor alone. He was blown away.”
Dave Schleicher is the Project One engineering technician. Dave takes Brian’s and Eric’s ideas and works out how to make them happen, which techniques to use, how to make vinyls for masking the frame for painting. In the case of complicated projects like the skeleton, this often means some clever sideway thinking.
“I had to go find an actual skull, and live-trace right off the skull–that was just crazy. We went to the University of Wisconsin and came up with all the drawings for the vertebrae, and I had to hand-trace them, label them, and match where they lined up. For the hips, the human ones weren’t working, so we had to use an X-ray from a dog’s hip!”
Dave is lost in folders and files on his desktop. The last ten years of special paint finishes and graphics flashes on the screen. The attention to detail, the complex engineering that turns a concept into a paint scheme, is extraordinary. And once the art and makes are complete, it’s up to the painter to bring the design to life on its carbon canvas.
“It’s sort of a layering technique. It’s a very artistic interpretation, the masks aren’t meant to be a schematic. Every time we develop a new design, we save the files, just because we might use some of it on another project. We’ve done a snake head, we have skulls…John Burke, Trek’s President, gave his wife a panda design bike, so we’ve got that. There we go, pandas!”
The same meticulous airbrushing used for the rare one-offs also applies to the Project One Signature Series schemes. Applying the Real Fire scheme to tubes and fork ends is around nine hours of work, all done by a single painter. Each Signature Series frame belongs to one artist, from start to finish, who signs his work at the end. Bob explains:
“We take it personally, because we know that one person has ordered this one frameset, this one bike. The frame already has an owner, written right on the tag. That owner is a person, someone who’s created this expression in the form of a bike. We build it and sign it, from one person to another–it’s tough to get more personal than that.”
BUILD YOUR ONE BIKE ON THE TREK FACTORY EXPERIENCE»